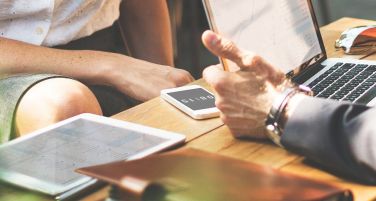
Logistics automation:
Trends and opportunities
The logistics industry has been impacted by digitalization and its effects on closely linked industries such as retail and the rise of e-commerce. The pace of change in logistics has been disrupted by supply chain issues across the globe in recent years. New economical reality have highlighted the urgency needed to ensure a cost-efficient recovery for the industry.
Since Covid lockdowns and other geo-political factors have affected global supply and movement of many goods, logistics management software is rapidly gaining traction in the supply chain industry. Employing technology allows businesses to improve efficiencies, reduce operational threats to profit margins and make significant cost savings. Organizations can manage and track shipments easily and accurately whilst improving customer services.
Businesses are already using warehouse management systems to automate stock management, manage increased volumes of goods, optimize storage and accelerate order fulfilment. However, in times of uncertainty, a resilient supply chain does not mean a series of automated standalone processes – organizations need end-to-end supply chain visibility and management that means operational inefficiencies can be quickly highlighted and rectified.
What is logistics automation?
Logistics automation eliminates the manual handling of repetitive tasks and allows processes to be efficiently managed, reducing the risk of human error.
From an operations perspective, logistics automation involves streamlining processes, improving transparency, accuracy and efficiency to standardize quality management and improve service levels. It can involve many areas of technology such as driverless transportation and smart transport centres (e.g. ports and warehouses).
Businesses that think strategically about logistics automation can successfully integrate their logistics management software into their entire digital ecosystem; it is this kind of digital-first business that can truly transform and automate process to improve the bottom line.
Why logistics automation is important. Industry trends
Accenture reports that 75% of Fortune 1000 companies have been impacted negatively or strongly negatively by Covid-19 supply chain disruptions. The logistics and transportation industry has been adversely affected with global container shipping rates reaching, on average, four to five times their 2019 levels – with some specific markets seeing even higher increases according to McKinsey data.
Senior stakeholders and C-level executives are under increasing pressure to control spiralling costs and maintain short-term ROI, with many aiming to improve the agility and resilience of their organizations whilst balancing this against risks. The supply chain has changed with 48% of supply chains becoming more complex in the last year due to a variety of factors including:
Geographical expansion and larger customer bases:
Ecommerce has given businesses the opportunity to expand globally but this means that the supply chain is more complex. Businesses must consider new territories and how to fulfil orders in new markets.
Diversification of supply and new sourcing strategies:
Many businesses are shifting from linear supply chains to more integrated networks to overcome sourcing issues. According to KPMG, businesses recognize the need to better equip their supply chains by identifying alternative trading partnerships so there is not one single point of failure. This adds complexity in the form of multiple interconnected partners that form a network that includes suppliers and potentially new services providers.
Delivery expectations:
Customers expectations have changed and it is now necessary to provide the status of an order and real-time delivery updates. As DHL highlights, logistics is becoming more diversified. An agile business which can pivot quickly is the key to maintaining the stability of the supply chain, but this does mean that supply chain management is more complex. Logistics software should address this challenge and help manage increasing complexity without the need for laborious manual processes and increased staffing costs.
To truly realize the benefits of logistics automation, organizations need to address the major challenge of not allowing supply chain systems to operate in isolation. The supply chain depends on external factors and must operate as part of a wider digital ecosystem to ensure optimization and the ability to make changes to respond to internal/external disruptive events, market conditions and changing strategies.
End-to-end logistics management and process automation is gaining more traction both large corporates and SMEs that are looking to reduce costs and increase efficiencies. Using API technology, organizations can now connect multiple systems to automate more complex business processes.
Six benefits of automating logistics
in your business
Although cost control and maximizing revenue is often the primary goal for implementing a logistics automation system, there are multiple benefits.
Logistics automation
drives cost savings
Logistics automation can reduce operational costs by ensuring the most efficient decisions are made throughout a process from efficient courier routing to choosing the most cost-effective carrier. Significant savings can be made through automated controls on freight spend / insurance payments and optimizing the load of each shipment. Automated stock inventory management can also reduce storage expenses and manage peaks in demand to ensure sufficient stock to fulfil orders.
Increased productivity and operational performance
By automating routine processes, businesses can use logistics software to maximize employee productivity and free up time to spend on revenue generating work.
Reduced human
errors
Logistics automation minimizes human error that can happen frequently with tasks that are repetitive and time sensitive.
service
Supply chain automation provides better visibility over order fulfilment, improving service quality and transparency for customers.
Clear, centralized data flow and data analysis
When market conditions are volatile, access to real-time data is essential to businesses that want to have competitive advantage. Real-time data allows organizations to improve planning and respond quickly to disruption, increasing resilience in the face of unexpected external events.
Scalability
and speed
Ecommerce has revolutionized how logistics and transportation operate by accelerating the speed at which products move along the supply chain to the end user, for example, through same-day delivery.
As consumer expectations have risen, businesses need to implement logistics process automation to handle order fulfilment without manual processes that cause delays and errors.
Barriers to effective change
According to a McKinsey study, 85% of respondents have inefficient digital technologies in their supply chains and only 14% of respondents have made sustained performance improvements.
Despite the many benefits of logistics automation, many organizations face barriers to making a positive change including:
Lack of digital strategy
Despite all the advantages of automation, true digital transformation is about more than simply automating a few business processes. A successful digitization spans different departments and considers a range of factors including optimizing business processes to overcoming resistance to cultural change. Digital strategy needs to become the foundation of business strategy and requires coordination across the entire organization. Focusing on one aspect and ignoring others risks wasting time, money and opportunity for real change.
Supply chain complexity
Complexity in the supply chain will continue to be a significant concern for supply chain leaders worldwide, especially when it comes to automation. 46% of supply chain leaders reported having a difficult time integrating functions across the supply chain—from manufacturing to end-customer deliveries. On the one hand automation is a promising way to manage increased complexity in the chain, but, at the same time, implementing the right technology can be seen to be adding to complexity and stress. For example, workflows can become fragmented as businesses migrate to new technologies as not everything can be changed simultaneously due to the need for business continuity.
Slow return on investment (ROI)
According to PWC estimations, profits in logistics are relatively low with EBIT margins generally ranging from 1% to 8%. Advanced logistic and transportation automation often requires significant financial investment, often costing thousands of dollars in annual fees for support, maintenance and upgrades. Once the new solution is live, it will take time to see a monetary return on that investment.
The companies that succeed in creating value begin with very clear and specific ROI goals, measure their performance against them and continuously iterate to hit targets. This results in cost savings, reduced inefficiencies, improved quality of customer service and productivity.
Cost savings
Reduced inefficiencies
Improved quality of customer service
Productivity
Wrong choice of technology
Lack of compatibility between existing hardware / software landscape and new technologies may also contribute to issues with realizing the benefits of automation. Businesses can suffer from adding new technology to an already-complex tech landscape without considering how the platform will fit into existing technologies and help to meet long-term strategic goals.
The ultimate goal for any newly acquired logistics and transportation software solution should be overall productivity and profitability improvement of the business.
Before deciding to implement any new technology, it should be evaluated based on several important criteria.
- How it helps to improve the overall productivity and profitability of the business
- How easily it can be integrated into the existing IT landscape
- How it helps to overcome vendor dependency
- Whether the technology is scalable and customizable
- How it helps to minimize costs
The top 5 logistics automation systems businesses
can implement today
Transport Management Systems (TMS) are the foundation of logistics automation. According to Gartner the scope of a TMS includes processes such as freight movements planning, freight rating and shopping across all transportation modes; selecting the appropriate route and carrier; freight bills and payments management.
Many of these processes can be partially covered by generic ERP systems or larger supply chain management (SCM) systems, however those systems are cumbersome and face problems in managing the ever-growing demands of complex and dynamic logistics processes. They lack agility to be able to integrate into larger workflows and adapt to changes fast enough to meet business needs. As a result, according to industry research 38 % of shipping companies and 67 % of 3PLs (Third Party Logistics companies) stated that they were investing in a transportation management system.
Transport management systems can improve planning efficiencies by automating dispatch. The number of less-than-truckload (LTL) shipments is growing and therefore, the ability to compare rates from multiple carriers within one system is critical to reduce cost per hundred-weight or cost per mile of freight movements. In multimodal transportation, TMS’ automate workflows among different cargo delivery stakeholders, managing all supporting administrative processes.
Another value that TMS can immediately bring to businesses is reducing the risk of failure to comply with regulations and potential exposure to legal penalties and monetary fines. Automating back-office processes helps to make sure that each shipment is properly documented and compliant.
In a broader supply chain context, TMS’ provides visibility over inbound material movements required for manufacturing schedules and improves customer service by providing better visibility for products movements.
Fleet management solutions
Fleet management has significantly changed in recent years. As businesses have become more concerned with their environmental footprint, many are looking at ways to monitor and manage their emissions. Roadside and in-vehicle sensors have made real-time fleet monitoring commonplace and created new opportunities for process automation.
Fleet management software is designed to improve fleet operations by automating core processes including a vehicle's location tracking, maintenance scheduling, driver management and route planning. Additionally, it can help to monitor emissions that degrade air quality, track hours of service (HOS) to stay compliant with regulations and improve driver safety. Fleet management solutions may also handle vehicle leasing/finance and insurance renewal.
Businesses can benefit from lower fuel consumption, reduced maintenance costs, optimized schedules, and reduced delays.
Who benefits from fleet management solutions?
It is a common mistake to believe that only large companies, operating hundreds of vehicles will benefit from deploying a fleet management solution. It is not the size of the fleet that matters. If core operational processes are relying on transportation, fleet management solutions ensure that each asset is used optimally and assist in time-consuming administrative tasks. This can influence overall business performance and ultimately, the bottom line.
Dispatch management software
It is now clear that the pandemic’s influence on buying behaviour and ecommerce has created a permanent shift, especially when it comes to demand for delivery services. This industry relies heavily on labour. With unprecedented growing volumes of work, it is becoming difficult to recruit and train enough staff as well as manage a large field workforce.
Dispatch management software can be used to manage vehicle coordination, equipment and automate workflows to fulfil orders or service requests. It can also automate people management such as overseeing drivers or technicians in the field and work orders assignment.
Using process automation in dispatch improves client service and enables more efficient logistics operations.
Supply chain visibility software
Supply chain visibility software provides a single source for tracking the entire logistics cycle from raw materials/components to procurement, distribution, transport and delivery to the customer. Depending on the type of business it may also include after-sales service.
Supply chain visibility solutions are used to overcome complexity in supply chain networks management, enabling strategic collaboration across internal operations and external partners.
Track & trace solutions an E&Y survey showed that more than 60% of supply chain executives reported that better visibility is their top priority for the next three years. Track & trace systems are the foundation of supply chain visibility. They allow real-time information on the whereabouts of a product throughout the entire supply chain and the ability to trace a product back to the place it was produced and with what materials. This is particularly beneficial in certain regulated industries such as pharmaceuticals.
As effective business operations require more transparency and visibility, track & trace solutions becoming important in other industries as well.
Where should
a business start?
Automation in transportation is often centered around consolidating cargo and calculating the optimal route for delivery according to each customer’s needs. The ultimate goal is to maximize the capacity of each vehicle and driver, reducing the cost of delivery under complex conditions.
There are many solutions in the market that are readily available to deal with that problem. Transport management systems usually support all methods of shipment including Full Truckload (FTL), Less than Truckload (LTL,) and mix of these two. However in a dynamic environment, there are challenges with TMS’ and transport planners can’t afford to rely on traditional, unsophisticated rules-of-thumb to optimize truckload shipments that are hardcoded into generic TMS’. With the growth of multimodal transportation, the industry needs new solutions that can automate planning and optimization, overcoming the complexity that is being generated around those processes.
When it comes to planning, many large and small companies are still relying on Excel spreadsheets and operations managers expertise to do the job. These laborious, manual processes require significant effort and prevent other processes from being automated. As the scale and complexity of models grow, many companies are looking for a way to overcome Excel dependency: this is the best place to start with automation.
How can Jmix help
automate logistics processes
Jmix is a single digital platform for creating business web applications in transportation logistics. Despite commercial off-the-shelf logistic applications the platform doesn't include a default business logic. Jmix powers up transportation companies to build customized applications according to the actual business objectives. In order to reduce the development complexity the platform includes a lot of basic objects out-of-the box including web application server with built-in database integration.
Developers get a set of high productivity tools and a rich catalogue of ready-to-use business components which significantly reduce time-to-market and development complexity. Jmix allows to create an extensive data model without writing a single line of code providing visual tools and development assistance. If the data model already exists in the legacy database - it can be easily reengineered into Jmix data model. Yo can migrate list of values, order backlog, location list, transportation resource list, customer and carrier lists and etc. to a new application with minimum efforts. Business logic can be implemented and adjusted in a working application "on the fly" with a built-in BPMN 2.0 designer. A dedicated Maps component performs easy-lifting of object allocating and transportation routing visualization.
Open platform architecture and a future-proof technology stack ensure that you can build a broad spectrum of applications and provide continuous business resiliency. When finished with development you get a perfectly shaped application which you own and control. Applications built with Jmix can be deployed on-premises or in the cloud without any licence spendings on end-users and deployments. Combining an open-source Java-based framework and per developer seat pricing Jmix truly helps to overcome vendor dependency, minimize costs on software delivery and ownership.
Use our business value assessment tool to get a ROI estimation comparing the platform against traditional development and popular low-code offerings.
Logistic automation FAQs
Spreadsheets are prone to errors
As the data held in Excel grows overtime, the propensity for mistakes in formulae increases; an error in a single cell can become very difficult to trace and fix before it causes a costly mistake.
Spreadsheets slow down digitalization and digital maturity
Spreadsheets are an outdated way to store data as they are not very scalable and can be unreliable (the larger the file, the greater the chance of the file becoming corrupted). By using multiple spreadsheets, data within an organisation is siloed and difficult to share across multiple teams and therefore Excel-based processes cannot be integrated into company-wide workflows.
Risk to organizational compliance
Information security can be at risk by using spreadsheets to store data as there is a lack of robust and secure entity management options. It is also difficult to enforce policies and track compliance.
The load planning process typically involves several modes of transportation, last-minute cargo changes and many other factors that need to be considered to ensure a timely and cost-effective delivery. Current trends indicate that growing complexity cannot be managed without proper digital tools. Multimodal transportation is the best example of where the outcome relies heavily on the system that is used to solve the problem. It is the most complex task which combines FTL and LTL transportation models. The most efficient way to manage this kind of logistics is by using an open-source platform in which each stakeholder can input information such as how to deliver the cargo, time and price. Algorithms can then process the suitable options and build an end-to-end route and quotation provided by various carriers for the customer
Jmix allow businesses to develop solutions that meet all their specific requirements including pre-requisites for external parties such as the ability to show cargo tracing data. This means that companies can create flexible solutions without compromising on flexibility or security.
More sophisticated workflows like this are possible with Jmix and add-ons. These add-ons enrich applications with additional functionality such as intuitive manipulation of spatial data and visual representations in the form of dashboards. An out of the box system cannot anticipate and be ready for every single requirement and therefore configurable, flexible platforms are more able to meet complex operational needs.
When companies opt for rapid application development platforms like Jmix to automate processes, there are many integration options. Large external carriers provide API tools for integrations which facilitate real-time information exchange, allowing businesses to compare prices and choose the best deals for cargo.
An enterprise license allows companies to add advanced enterprise features and costs $150 per month for one developer. It includes geo-information system features, visual BPMN&DMN modeler, BPM for internal automation and many other features that will support quick application development. As Jmix is open-source it accelerates speed of innovation without vendor lock-in.
Customer Stories
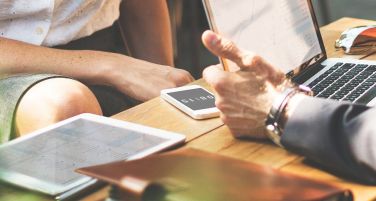
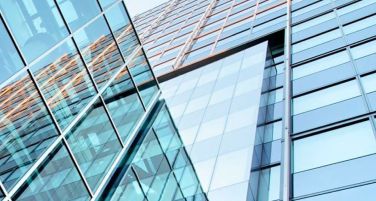
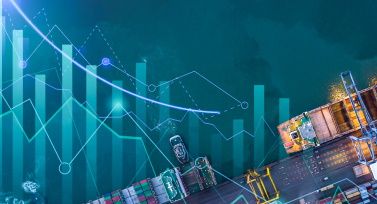